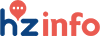
Numerical and experimental investigation on formation of the film for different die lip configurations in lithium-ion battery electrode slot-die coati
2024-03-25 08:51
A recent research proves that a smaller coating gap that controls the upstream meniscus between the upstream die edge and the slot exit is beneficial to coating consistency and helps to reduce edge defect formation.
Researchers found that the use of different die designs in slot die coating of lithium-ion battery electrodes has significant effects on coating consistency and the development of edge defects. Source: Adobe.Stock
The slot-die coating is the most commonly used manufacturing method for producing lithium-ion battery electrodes. However, how to achieve high surface consistency for electrodes still confronts one challenge. In this research, the slot coating processes with different die lip configurations were carefully investigated using numerical and experimental methods. The motion pattern, internal flow structure of the coating bead, and coating uniformity were explored during the coating process of lithium battery cathode slurry. The low-flow limit at different coating gaps was also determined by combining the viscous capillary model and numerical methods, which was in good agreement with experimental results.
The results showed that a smaller coating gap controlling the upstream meniscus between the upstream die lip and slot exit was favorable to the coating uniformity. For the same thickness films, a larger coating gap was apt to increase formation of edge defects. However, the coating speed had little effect on the edge height. The evolution of flow structure for the coating bead (parabolic–sharp angle–diagonal) under different processes was investigated by tracking the particle trajectories during the coating process. It can provide theoretical guidance for the fabrication of high-quality electrodes.
The study has been published in Journal of Coatings Technology and Research, Volume 21, Issue 1, 03 January 2024.
More Hzinfo
- Anhui Hechen Launches 80,000-Ton Paint Tech Upgrade; Qigu Group Deploys Multi-Dimensional Strategy Amid Market Transformation
- The "Environmental Impact Report Form for the 80,000 Tons/Year Paint Optimization and Upgrade Project" of Anhui Hechen New Material Co., Ltd. was officially accepted for public announcement.
-
2025-07-10
- Flint Group expands Italian resin facility for NC-free inks
- Flint Group has expanded its resin production site in Caronno, Italy, to strengthen supply security for nitrocellulose-free inks used in flexible packaging. The investment responds to rising demand fo
-
2025-07-10
- Chemetall site in China receives recognition from Pinghu Dushan Port government for its commitment to drive sustainability
- Chemetall’s largest production site worldwide powered by 100% renewable electricity
-
2025-07-10