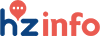
Covestro to Invest in Pilot Plant for Recycling of Elastomers
2024-12-17 08:47
Pilot plant will be built in Leverkusen, Germany
Covestro announced plans to build a pilot plant for recycling of elastomers. The investment in the double-digit million euro range is used to fund the development and construction project of the state-of-the-art pilot plant at Covestro's site in Leverkusen, Germany. The construction is estimated to take about one year until technical completion.
This technological development to recycle Vulkollan® marks an important step towards more sustainability in the elastomers industry. The technology enables to not only recycle a mass fraction of more than 90% of the end-of-life material like forklift tires, but also to reduce the carbon footprint by up to two thirds compared to virgin material.
“The pilot plant and with it our commitment to proving the feasibility of recycling for elastomers demonstrates our clear commitment for circular solutions and marks an important milestone for our elastomer products”, states Dr. Thomas Braig, Head of the Elastomers business entity. “With the successful scale-up of this new recycling process we address the demand of our customers for end-of-life solutions and carbon footprint reduction while assuring the high quality of our elastomer products. At the same time, this pilot plant is an invitation for players along the value chain to cooperate on developing a circular setup and the reverse value chain for end-of-life materials.”
Covestro customers use Vulkollan systems to mold parts for many applications with a high demand for durability and performance. Typical applications for parts made of Vulkollan are wheels for forklifts, bumper elements in railways and vibration control elements and jounce bumpers in cars. The excellent quality of Vulkollan allows more sustainable and cost-efficient operation of the target application through longer lifetime, longer maintenance intervals and less unplanned shutdowns. Due to the high yield of the recycling process, end-of-life Vulkollan materials can be re-introduced into new automotive jounce bumpers and forklift tires via a mass balancing approach.
The new chemical recycling process is a game-changer for the elastomers industry. Unlike mechanical recycling methods, this approach breaks down elastomeric end-of-life material into its chemical building blocks, to obtain purified monomers that can be re-used for these materials with known and proven quality.
"The new chemical recycling process addresses the unique challenges of elastomer materials, which are trusted to be very resistant and long lasting. Downcycling is not an option for this high-performance application,” explains Markus Dugal, Head of Process Technology at Covestro. “This technology allows us to recycle a high mass fraction of the end-of-life material and, in this way, to reduce the environmental impact of our elastomer production. It is a testament to Covestro's innovative spirit."
The pilot plant will play a crucial role in refining the recycling process beyond lab scale, testing the process with various waste streams and with various end-of-life materials. It will also serve as a platform for Covestro to engage with potential project partners and customers, paving the way for the development of a larger commercial recycling plant in the future.
Covestro's investment in elastomers recycling aligns with its broader strategic goals of reducing environmental impact, promoting circular economy principles, and maintaining its position as an innovation leader in the polymer industry. The company invites potential partners and customers interested in circular elastomer solutions to engage in discussions about future collaborations and applications and prove the environmental benefit of the solution along the value chain.
More Hzinfo
- Recommended products: Stearic acid modified calcium carbonate TL-906A-1
- TL-906A-1 adopts a special process to make stearic acid into a stable and unique low viscosity aqueous lotion.
-
2025-01-10
- European Commission adopts ban on BPA in all food contact materials
- Following an 18-month phase-out period, BPA will no longer be allowed in any products that come into contact with food or drink.
-
2025-01-10
- Recommended products: Anti slip and wear-resistant wax lotion TL-204-40
- TL-204-40 has strong polarity, has little effect on adhesion and heat sealing, meets food contact requirements, and can be used in adhesives and heat-sealing coatings.
-
2025-01-09